How to get good concrete mix
For small residential structures the owner won’t have a consulting engineer to supervise the work and they solely depend on the contractor and trust them blindly. Unfortunately most of the contractors aren’t trustworthy. Defects in concrete are very hard to find for a layman and here are some important things to look for while concreting.
Check for exact specifications
Ask the contractor/engineer to give you a copy of concrete mix design. Most of the contractors don’t do proper mix designs and you don’t skip this one. Doing a mix design specifically for your project is better. Concrete cubes tested for strength from a good lab.
Check for materials
Checking the quality of materials in a lab by an engineer is mandatory. Check for the batch number/manufacturing date of cement. If the cement is more than 3 months old reject the cement. Test aggregates for the following
- Strength
- Durability
- Impact strength
- Shape test
- Sieve analysis
Shuttering
Don’t allow the contractor to bring scrap wood for shuttering. Insist for steel props other than scrap wooden props of irregular size and shape. Providing containment screens will avoid spill of materials. Joints in shuttering must not leak cement slurry which leads to bleeding. Check for shuttering mistakes such as misalignment, gaps in form-work, irregular shape etc.
Clear cover for concrete
Clear cover for concrete is very important because inadequate cover results in reinforcement exposure which leads to corrosion and cracking. Cover blocks or spacers are used to give clear cover for concrete and the cover blocks must be of the same grade of concrete i.e if the concrete is of M20 then cover blocks must also be M20 grade. In every 1 square meter there must be 4-5 cover blocks or spacers. Clear cover for concrete will be 25-40 mm. Crushing of cover blocks due to weight happens and before pouring concrete damaged blocks should be removed.
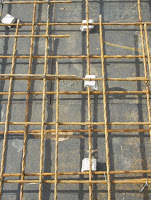
Check for reinforcement
Insist on anti rust coated reinforcement steel bars. Properly inspect reinforcement for any irregularities, bend and rust. If overlapping done then check for overlapping length because it must be 60d (Diameter of steel bar multiplied by 60 in mm). Check for alignment of lateral reinforcement and ensure proper ties, consult with the reinforcement drawings.
Mixing and pouring concrete
The minimum quantity of cement by IS standards is 350 kg/ cubic meter i.e 7 bags per cubic meter. Count the number of bags used by the contractor and ensure they use the right quantity of cement. Only potable water should be used to mix concrete because water containing impurities like chlorides and other chemicals will react with cement. The following apparatus must be present at site
- Cube molds of standard size ( Min. 3 molds)
- Slump test apparatus
Take cube samples randomly after mixing and compacted by hand. These cube samples should be cured for 7 days and tested at a lab for compressive strength. For M20 mix the cube strength must be not less than 13.5 N/mm2 at 7 days.
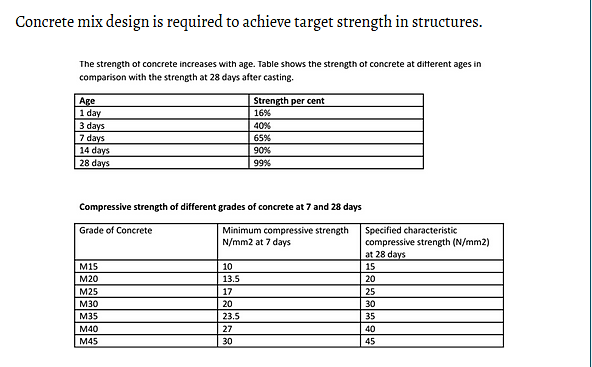
Slump test to be done randomly for different batches because for RCC the concrete must not be flowing or too hard. The optimum water cement ratio is between 0.45 – 0.7 and anything above 0.7 will decrease the strength. For the ease of work-ability they will add too much water which will decrease the strength.
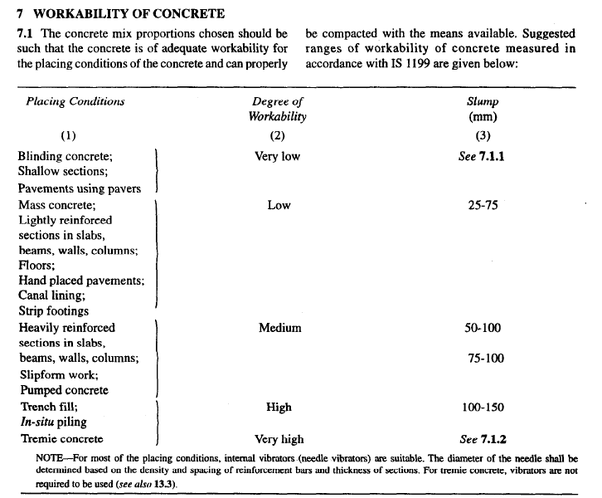
Ready mix is always better because it is not always possible to monitor the mix on site and the minimum order quantity of ready mix concrete is 7 m3.
Compaction of concrete
Compaction is very important for the strength and durability of structure and to avoid future maintenance. Normally done by needle vibrators. Make sure 2 needle vibrators are present at site with at least 2 spare Needles and enough fuel to operate. Double check these things because once the concrete is placed initial setting is within 30 minutes. At beam column joints needle vibrator cant be placed, there manual compaction with tamping rod must be ensured strictly. These are the areas they will skip compaction and it will adversely affect the durability and strength of the structure.
For further reading check out https://en.wikipedia.org/wiki/Concrete
Leave a Reply